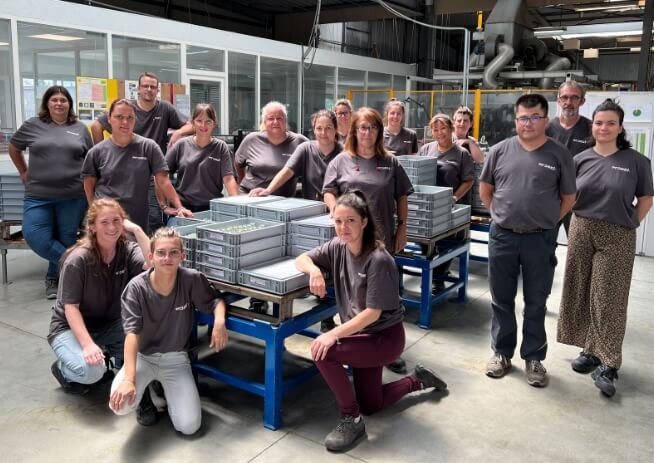
A NEW WAY OF THINKING ABOUT HYDRAULIC FITTINGS
Our aim is to simplify hydraulic fittings and join forces with other engineers to help improve the overall design of their systems and reduce our industry’s carbon footprint. For this, we have standardized our upstream processes, allowing us to streamline the manufacturing workflow. Fewer sub-assemblies means less steel. Moreover, our hydraulic fittings are much simpler in their design (less space, less weight), resulting in a significantly reduced carbon footprint.
CUSTOMER SERVICE ABOVE ALL
erasch has a small team of 35 highly-skilled employees, all focused on customer service. QRM (Quick Response Manufacturing), is the keystone of our organization, and aims to reduce lead times throughout the entire process, from quotation to delivery. To achieve this, we have put together versatile teams and created cross-functional departments. The result is unrivalled responsiveness, with lead times ranging from 3 to 5 weeks for normal orders, and up to 72 hours for urgent orders, depending on the product.
That’s how we do it!
A DESIGN OFFICE THAT PROVIDES CUSTOMER ASSISTANCE
Our design office is at the heart of our organizational structure and is fully integrated into the customer service department. In addition to providing 3D-designs using our powerful online configurator, solverasch.com, our design office ensures your queries are efficiently relayed to our manufacturing facility. From one design office to another – erasch works at an eye-to-eye level with hydraulic engineers designing hydraulic connections for mobile machines.
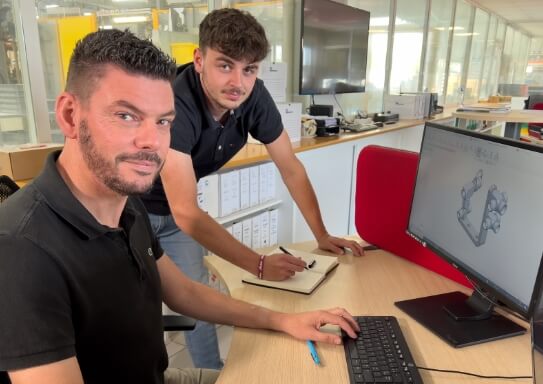
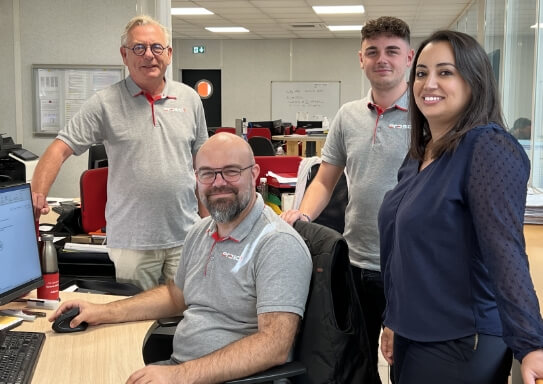
PRODUCTION FACILITY
The production facility at erasch works at 30% overcapacity, allowing us to respond extremely quickly to any manufacturing requests that may arrive in “urgent” mode.
At erasch, we are able to get everything done in-house, whether it be drilling (3 stations), soldering (3 stations), crimping, assembly or inspection.

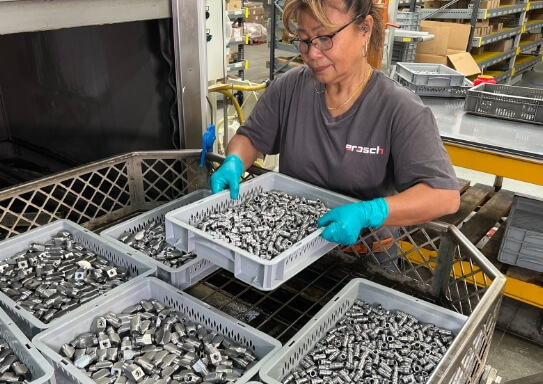
LOGISTICS SERVICES
At erasch logistics, we have around 500 bar-turned sub-assemblies in stock, allowing us to offer millions of possible configurations. And thanks to our QRM (Quick Response Manufacturing) approach, we can guarantee delivery within 3 to 5 weeks for normal orders, and within 72 hours for rush orders, depending on the product.
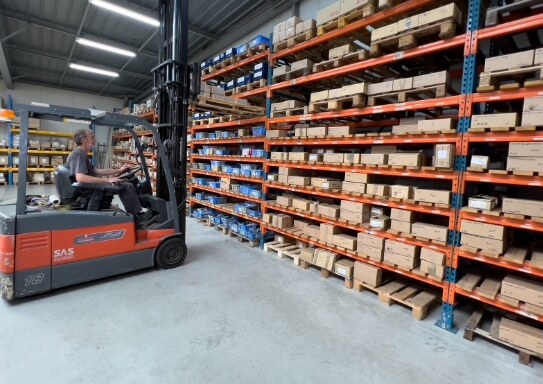
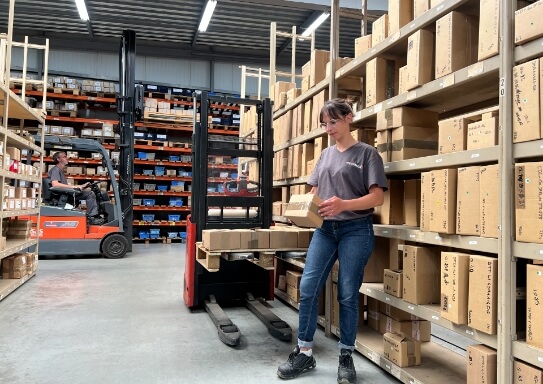
OUR NETWORK OF EXPERTS

Digital – Quentin Jouet – Montagne bleue
We create customised digital solutions to meet our company’s challenges. The Solverasch configurator is designed to simplify the day-to-day work performed by erasch‘s design office and its customers.
erasch is a trusted partner to its customers, with a strong commitment to the human, technical and environmental aspects of its business.
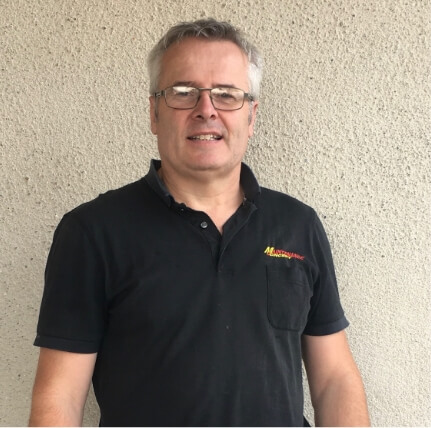
Maintenance adaptation machine – Jérôme Boré – Maintenance concept
We work with our customers to solve any technical or maintenance problems affecting their production machines, with the aim of enhancing productivity and working conditions.
I’ve been working with erasch for 16 years now and we’ve built up a trusting relationship. I’ve enjoyed the time I shared with the friendly management and team.
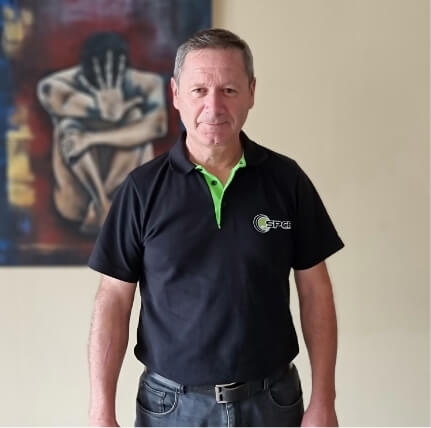
Treatment and parts cleanings – Pascal Serazin – SPCB
Specialized chemicals to treat ferrous and non-ferrous metal surfaces in preparation for organic coating or electroplating and to filter and remove effluents from industrial processes.
It was my pleasure to personally help erasch with their chemical baths. A passionate and cheerful team!
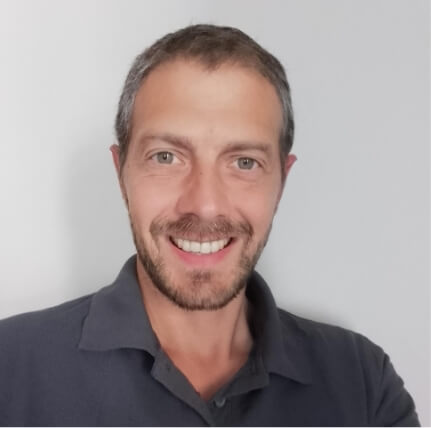
Brazing – Richard Tomasi – CETIM
I work with manufacturers on multi-material assembly projects involving brazing, welding and bonding.
erasch‘s structure is quite agile, enabling us to work together in a flexible way to meet the various brazing challenges we are facing at any given time.
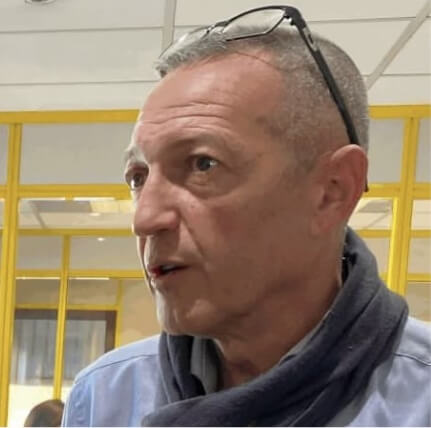
Bar turning – Stéphane Bonafedi – H.BOURGEAUX et Fils
30 years of managerial experience producing technical parts for the bar-turning industry.
At erasch, their corporate strategy is shaped by their market-driven approach, strengthened by their highly responsive and friendly team, exceptional service levels, and cutting-edge digital tools.
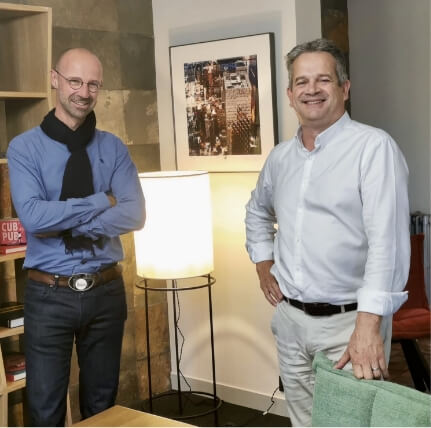
Communication – Yannick Le Cléarc’h & Jean-Charles Saunier – B17 Communication
We partnered with erasch to design and execute its communication roadmap.
With its simple solutions that help reduce the industry’s carbon footprint, erasch‘s hydraulic fittings are well worth the hype. erasch is leading the entire industry in the right direction.